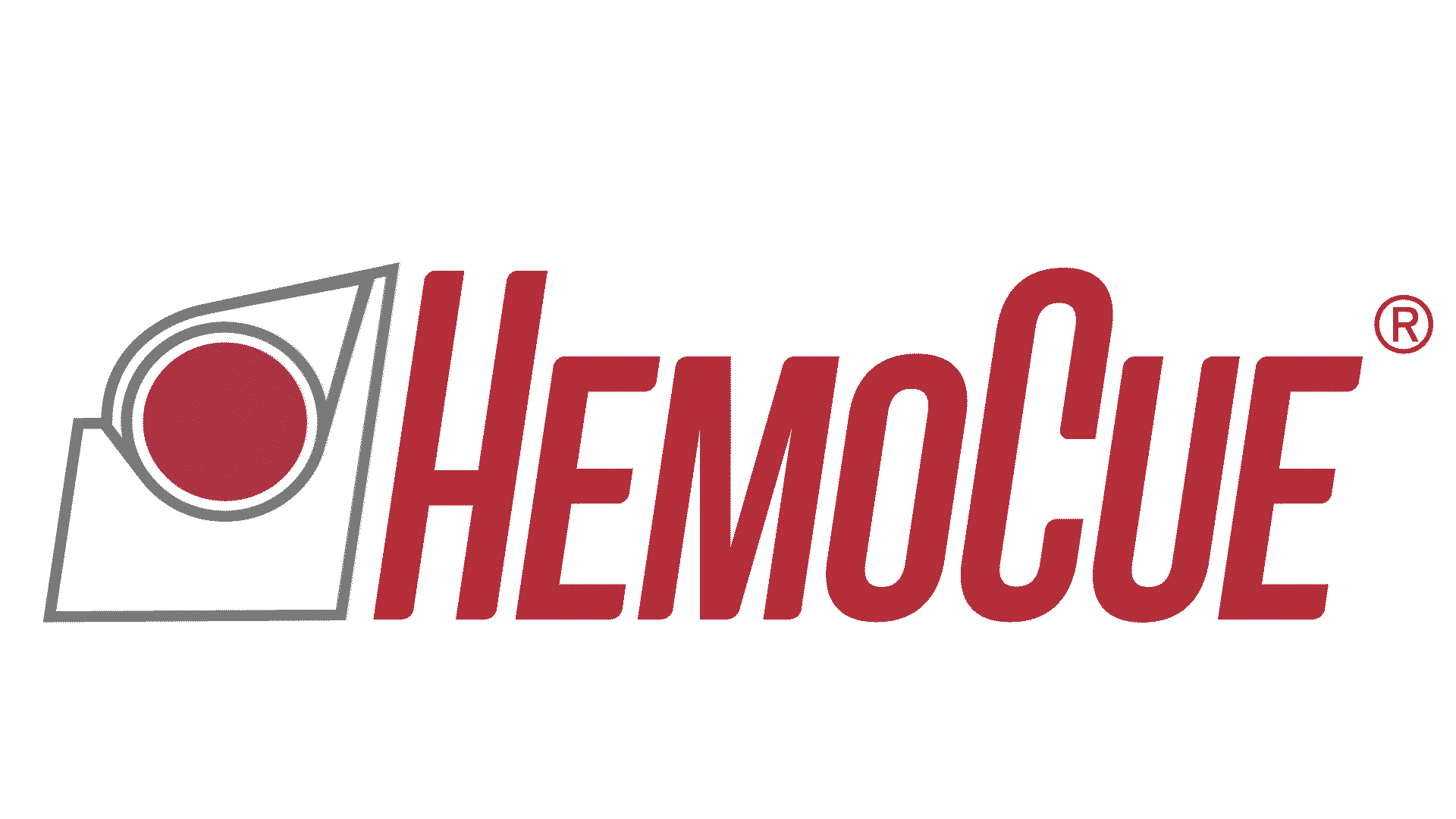
Accuracy is in our DNA.
Always has been, always will be.
Since day one, we’ve had a passion for accuracy
HemoCue’s founders were dedicated to accuracy. When they realized that hemoglobin results were often inaccurate, they vowed to find a better way.
Their devotion to accuracy still thrives at HemoCue. You might say that
accuracy is in our blood (pun intended!). Because we know how much it matters.
Our customers rely on our products to be precise every time they use them, so we insist on accuracy in everything we do. We are pleased to share some examples below.
Read about how it all started, how our operations teams went above and beyond to stay on time, and what it takes to maintain precision at a molecular level.
ON-TIME IN THE WORST OF TIMES
HemoCue’s operations teams overcame unprecedented challenges during COVID
Maintaining on-time delivery and keeping to accurate, meticulously planned schedules is always challenging. During a global pandemic, it can be nearly impossible.
COVID-19 created supply chain issues around the world. Companies were strained to the breaking point to obtain parts needed to fulfill orders.
HemoCue was no different, but came up with inventive ways to keep their deliveries accurate.
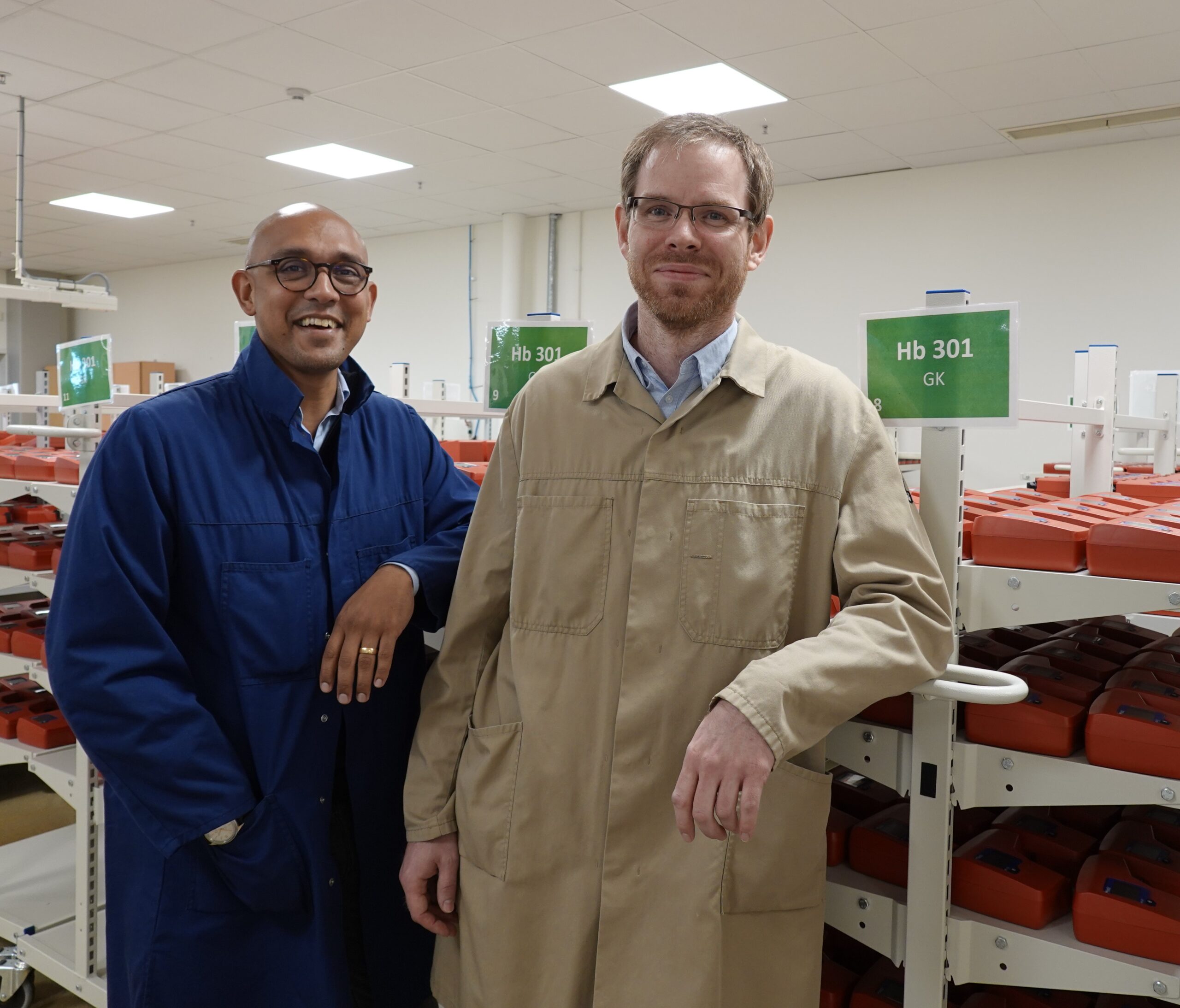
ON-TIME IN THE WORST OF TIMES
HemoCue’s operations teams overcame unprecedented challenges during COVID
Maintaining on-time delivery and keeping to accurate, meticulously planned schedules is always challenging. During a global pandemic, it can be nearly impossible.
COVID-19 created supply chain issues around the world. Companies were strained to the breaking point to obtain parts needed to fulfill orders.
HemoCue was no different, but came up with inventive ways to keep their deliveries accurate.
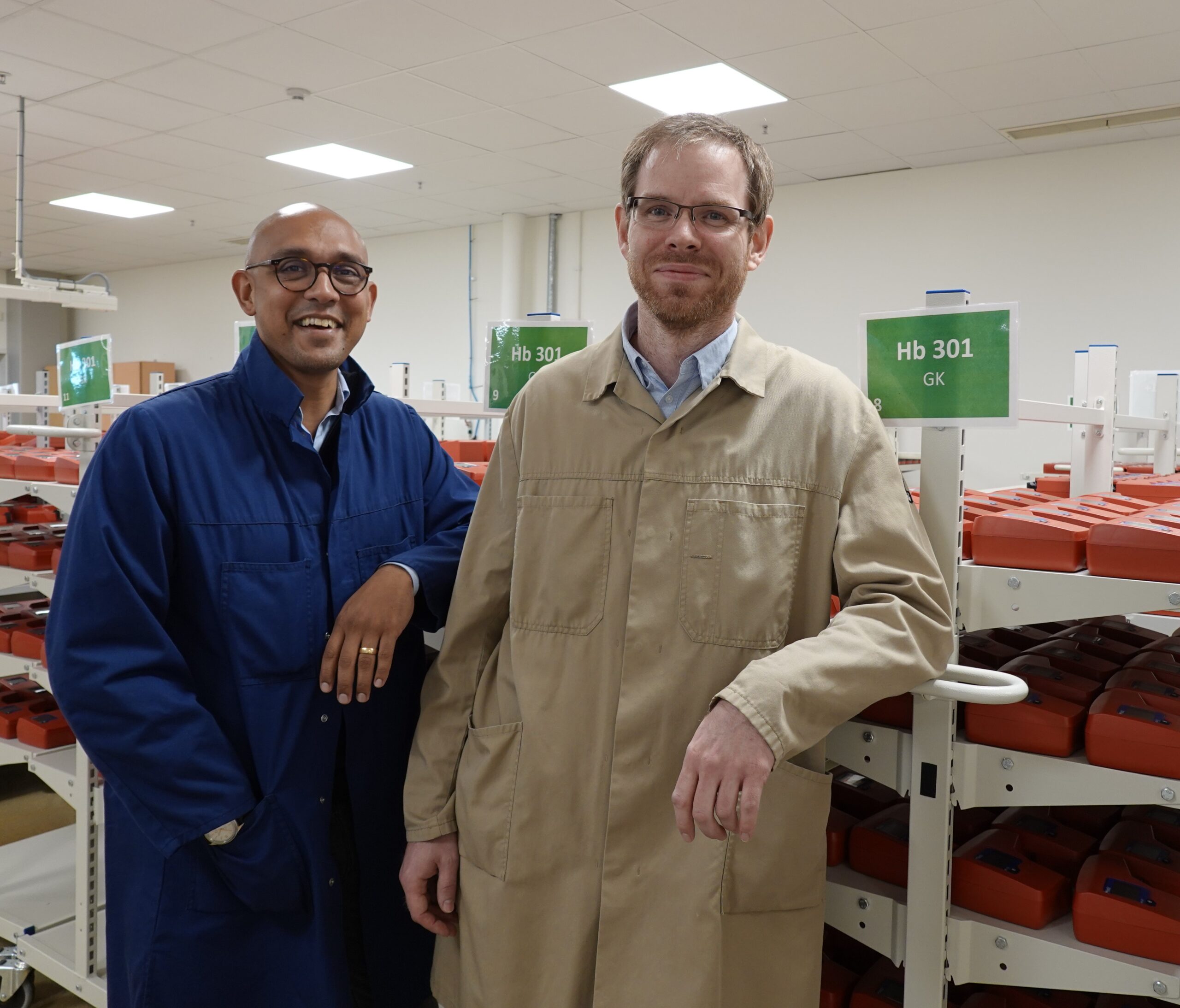
When the pandemic started, Rikard Fredriksson and Andreas Ekdahl headed up HemoCue’s Operations. They knew that COVID precautions for workplace safety and supply chain disruptions could have serious implications on the ability for HemoCue to deliver its products on time. When asked why delivering on time was so important, Rikard and Andreas both had a look of total incomprehension on their faces. Finally Andreas simply replied: “Why is it important to breathe?” Delivering on time and meeting obligations is so ingrained in the mentality of HemoCue’s operations teams, that it is as natural as breathing. Because the stakes are high. “Our customers rely on our products to help save people’s lives,” said Rikard. “We take that responsibility seriously and so it is not an option to be late.” In the summer of 2021, in the depths of the pandemic, the HemoCue team was expecting delivery of a specific electronic component, a touch controller for their 201 DM analyzer. Their supplier had confirmed a date, but then, just before the planned delivery, HemoCue was informed that a delay was expected. The new delivery date was April 2024. So, Andreas and the procurement team looked for an alternative supplier. No luck. They had to find another way. True to the entrepreneurial spirit of HemoCue, they decided that, if they couldn’t buy the specific component, they would need to redesign the product to make it work with one that was available. A small team was quickly assembled consisting of people with the required skill sets from multiple departments. R&D and product development teams found a new component and redesigned the analyzers electronics and firmware. Procurement sourced materials, while the operations team, together with their contract manufacturer, tackled the job of building prototypes and producing components based on the new design. Within two months, the team had built a working prototype, successfully conducted the required design verifications, received market validation, and began producing new analyzers. Another major challenge that HemoCue faced courtesy of COVID was labor shortages. The company established strict regulations to ensure the safety of employees and to avoid contaminating equipment used during production. The requirements made for a safe environment but created staffing challenges for production teams. The solution was to cross-train the teams to offer more flexibility. Previously, HemoCue’s production teams were divided into product specialties, which made it difficult to quickly adapt if people were out sick. The production teams worked to build a more flexible workforce in a series of workshops involving associates from all areas of production. At the start of the process, only 5% of the production team was cross-trained. The goal of the project was to increase that to 25%, but that was quickly surpassed. Now 40% of the production workforce is cross-trained and flexible. “Cross training and the flexibility of our associates was our savior during COVID,” said Rikard. “Not only did it keep us producing on time, but it also created new opportunities in job rotation for our teams and increased job satisfaction.”On-time delivery is as natural as breathing
Can’t get components? No problem, we’ll make them ourselves
Stringent safety regulations require a flexible workforce
When the pandemic started, Rikard Fredriksson and Andreas Ekdahl headed up HemoCue’s Operations. They knew that COVID precautions for workplace safety and supply chain disruptions could have serious implications on the ability for HemoCue to deliver its products on time. When asked why delivering on time was so important, Rikard and Andreas both had a look of total incomprehension on their faces. Finally Andreas simply replied: “Why is it important to breathe?” Delivering on time and meeting obligations is so ingrained in the mentality of HemoCue’s operations teams, that it is as natural as breathing. Because the stakes are high. “Our customers rely on our products to help save people’s lives,” said Rikard. “We take that responsibility seriously and so it is not an option to be late.” In the summer of 2021, in the depths of the pandemic, the HemoCue team was expecting delivery of a specific electronic component, a touch controller for their 201 DM analyzer. Their supplier had confirmed a date, but then, just before the planned delivery, HemoCue was informed that a delay was expected. The new delivery date was April 2024. So, Andreas and the procurement team looked for an alternative supplier. No luck. They had to find another way. True to the entrepreneurial spirit of HemoCue, they decided that, if they couldn’t buy the specific component, they would need to redesign the product to make it work with one that was available. A small team was quickly assembled consisting of people with the required skill sets from multiple departments. R&D and product development teams found a new component and redesigned the analyzers electronics and firmware. Procurement sourced materials, while the operations team, together with their contract manufacturer, tackled the job of building prototypes and producing components based on the new design. Within two months, the team had built a working prototype, successfully conducted the required design verifications, received market validation, and began producing new analyzers. Another major challenge that HemoCue faced courtesy of COVID was labor shortages. The company established strict regulations to ensure the safety of employees and to avoid contaminating equipment used during production. The requirements made for a safe environment but created staffing challenges for production teams. The solution was to cross-train the teams to offer more flexibility. Previously, HemoCue’s production teams were divided into product specialties, which made it difficult to quickly adapt if people were out sick. The production teams worked to build a more flexible workforce in a series of workshops involving associates from all areas of production. At the start of the process, only 5% of the production team was cross-trained. The goal of the project was to increase that to 25%, but that was quickly surpassed. Now 40% of the production workforce is cross-trained and flexible. “Cross training and the flexibility of our associates was our savior during COVID,” said Rikard. “Not only did it keep us producing on time, but it also created new opportunities in job rotation for our teams and increased job satisfaction.”On-time delivery is as natural as breathing
Can’t get components? No problem, we’ll make them ourselves
Stringent safety regulations require a flexible workforce
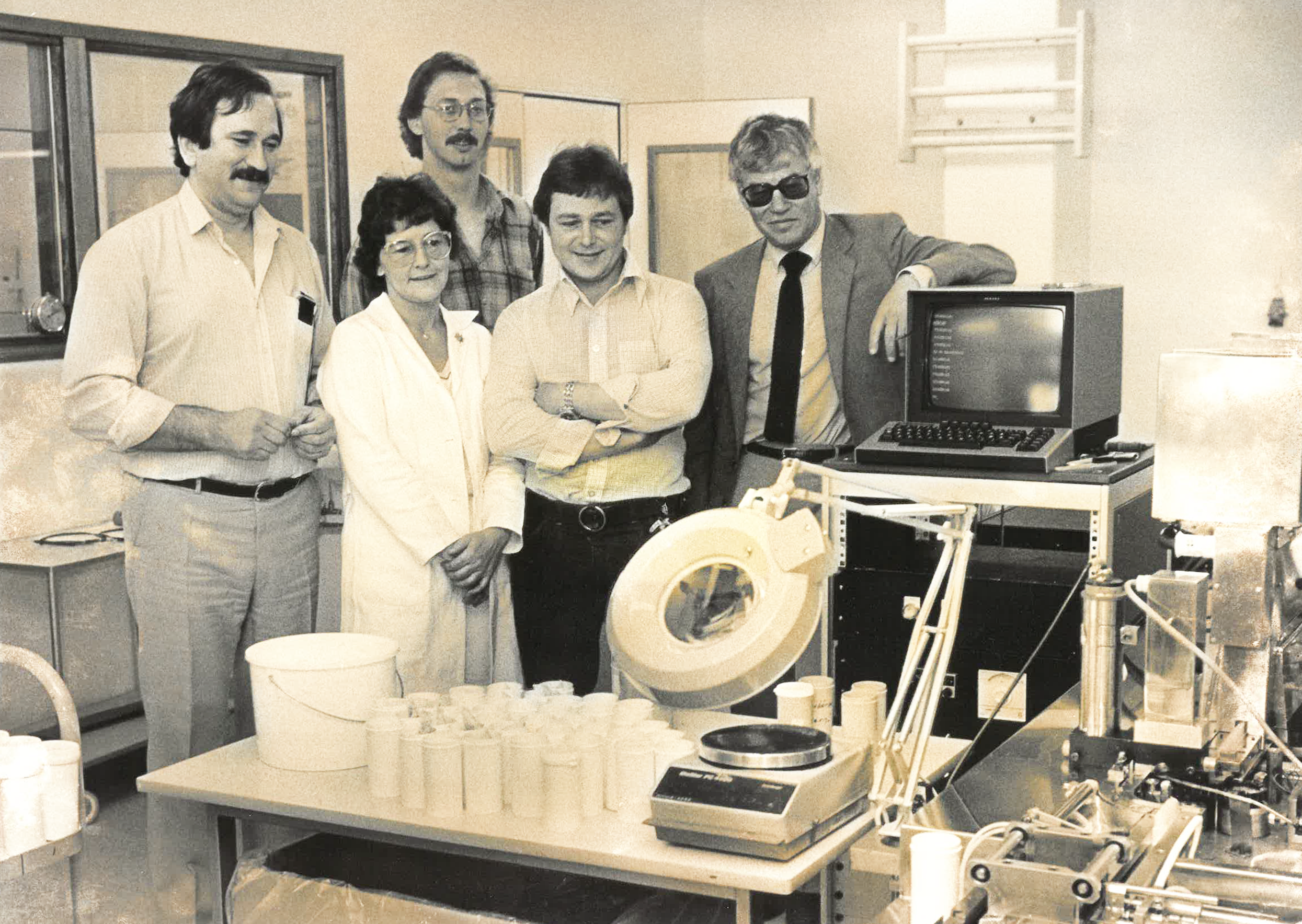
THE QUEST FOR IMPOSSIBLE ACCURACY, PART 1: THE DREAM
How cuvettes produced with unprecedented precision went from dream to reality
The idea was simple. HemoCue’s founders, Jan Lilja and Sven-Erik Nilsson, wanted to produce microcuvettes that could draw in a sample of blood to be analyzed by a portable photometer.
The problem was that the microcuvettes had to be manufactured with seemingly impossible precision to ensure accurate measurement. Yet, Sven-Erik and Jan were not scared by the impossible. And their quest for impossible accuracy has since become an integral part of everything we do at HemoCue.
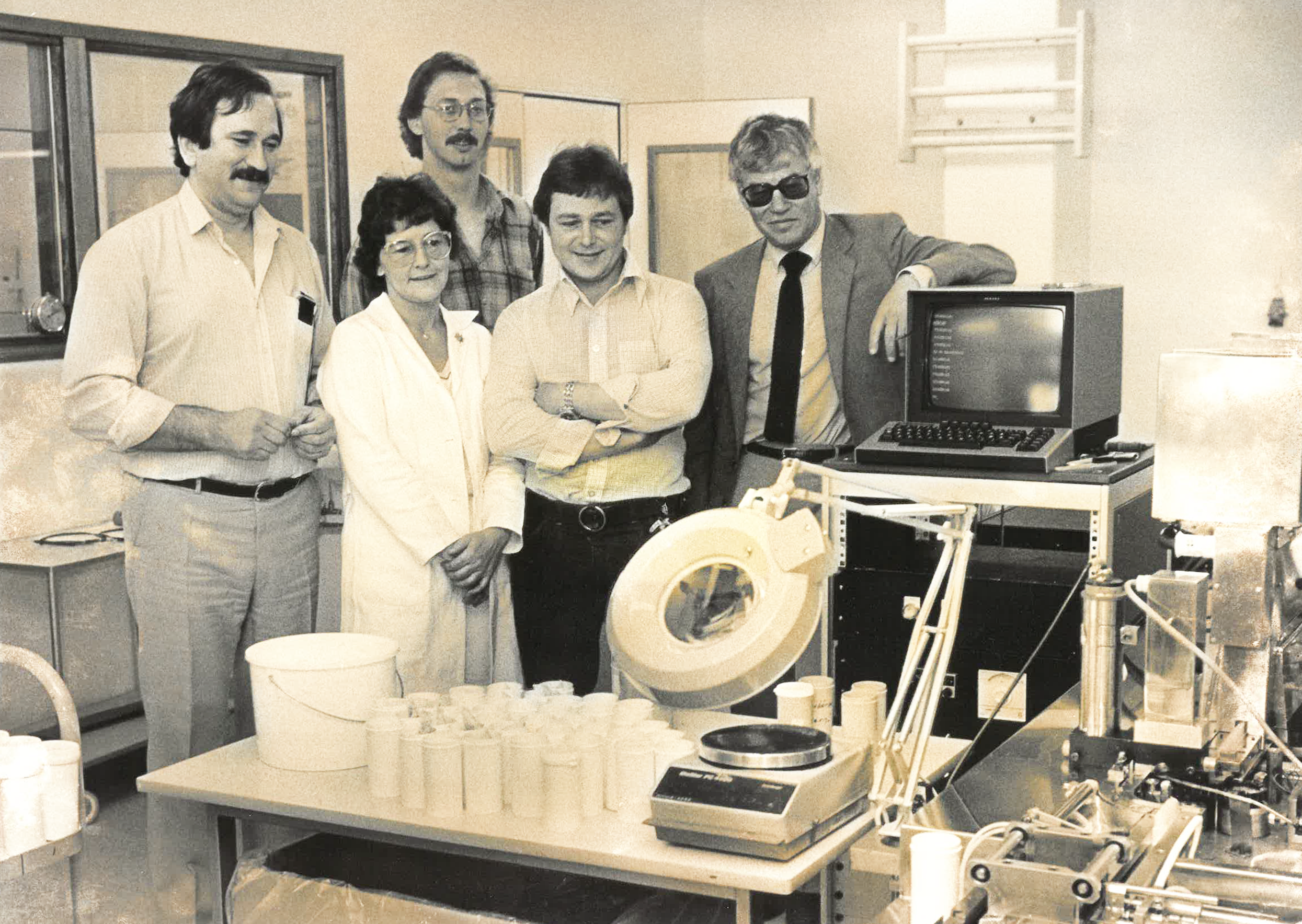
THE QUEST FOR IMPOSSIBLE ACCURACY, PART 1: THE DREAM
How cuvettes produced with unprecedented precision went from dream to reality
The idea was simple. HemoCue’s founders, Jan Lilja and Sven-Erik Nilsson, wanted to produce microcuvettes that could draw in a sample of blood to be analyzed by a portable photometer.
The problem was that the microcuvettes had to be manufactured with seemingly impossible precision to ensure accurate measurement. Yet, Sven-Erik and Jan were not scared by the impossible. And their quest for impossible accuracy has since become an integral part of everything we do at HemoCue.
Sven-Erik and Jan had exacting specifications for the microcuvette, measured in thousandths of millimeters. There was virtually no room for error. The tolerances (that’s engineer lingo for the permissible variation in measurements) had to be within just a few micrometers. No manufacturer would take on the task. They said it couldn’t be done, that the tolerances were impossible to achieve. On top of that, the plastic polymers to be used were thought to be too unstable and would be negatively affected by external factors. But Jan and Sven-Erik believed it could be done. So, they went back to their lab and, after months of trial and error, they built a machine that could produce the cuvettes. Their solution involved using an injection molding process with extremely precise molds – so precise that they had to be meticulously polished at a molecular level under a microscope. The achievement that was among the first of its kind. And while the molds are no longer polished by hand under a microscope, the general concept is still being used today to produce more than 140 million cuvettes each year.Tolerances measured in micrometers
Nope. Can’t be done.
We’ll see about that.
Sven-Erik and Jan had exacting specifications for the microcuvette, measured in thousandths of millimeters. There was virtually no room for error. The tolerances (that’s engineer lingo for the permissible variation in measurements) had to be within just a few micrometers. No manufacturer would take on the task. They said it couldn’t be done, that the tolerances were impossible to achieve. On top of that, the plastic polymers to be used were thought to be too unstable and would be negatively affected by external factors. But Jan and Sven-Erik believed it could be done. So, they went back to their lab and, after months of trial and error, they built a machine that could produce the cuvettes. Their solution involved using an injection molding process with extremely precise molds – so precise that they had to be meticulously polished at a molecular level under a microscope. The achievement that was among the first of its kind. And while the molds are no longer polished by hand under a microscope, the general concept is still being used today to produce more than 140 million cuvettes each year.Tolerances measured in micrometers
Nope. Can’t be done.
We’ll see about that.
THE QUEST FOR IMPOSSIBLE ACCURACY, PART 2: PRECISION PRODUCTION
Making cuvettes to exact specifications requires timing, rhythm, and extreme attention to detail
HemoCue micro-cuvettes look deceptively simple. They are clear plastic rectangles with what resembles a bird’s eye and curved beak sticking out of one side. But the process involved in making them is exceptionally complex and is the result of 40 years of refinement.
More than 140 million cuvettes are produced every year, and each one must be exactly alike.
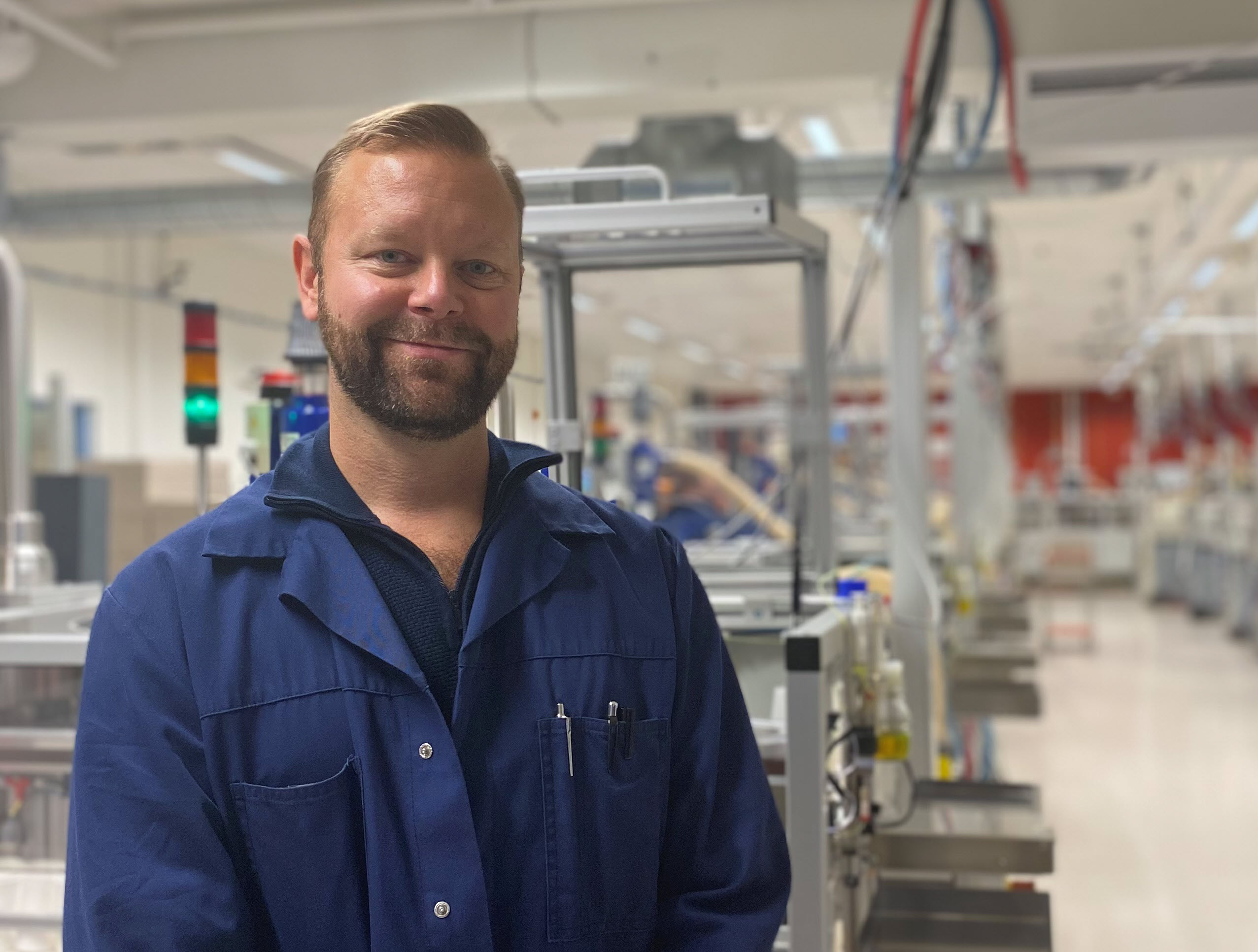
THE QUEST FOR IMPOSSIBLE ACCURACY, PART 2: PRECISION PRODUCTION
Making cuvettes to exact specifications requires timing, rhythm, and extreme attention to detail
HemoCue micro-cuvettes look deceptively simple. They are clear plastic rectangles with what resembles a bird’s eye and curved beak sticking out of one side. But the process involved in making them is exceptionally complex and is the result of 40 years of refinement.
More than 140 million cuvettes are produced every year, and each one must be exactly alike.
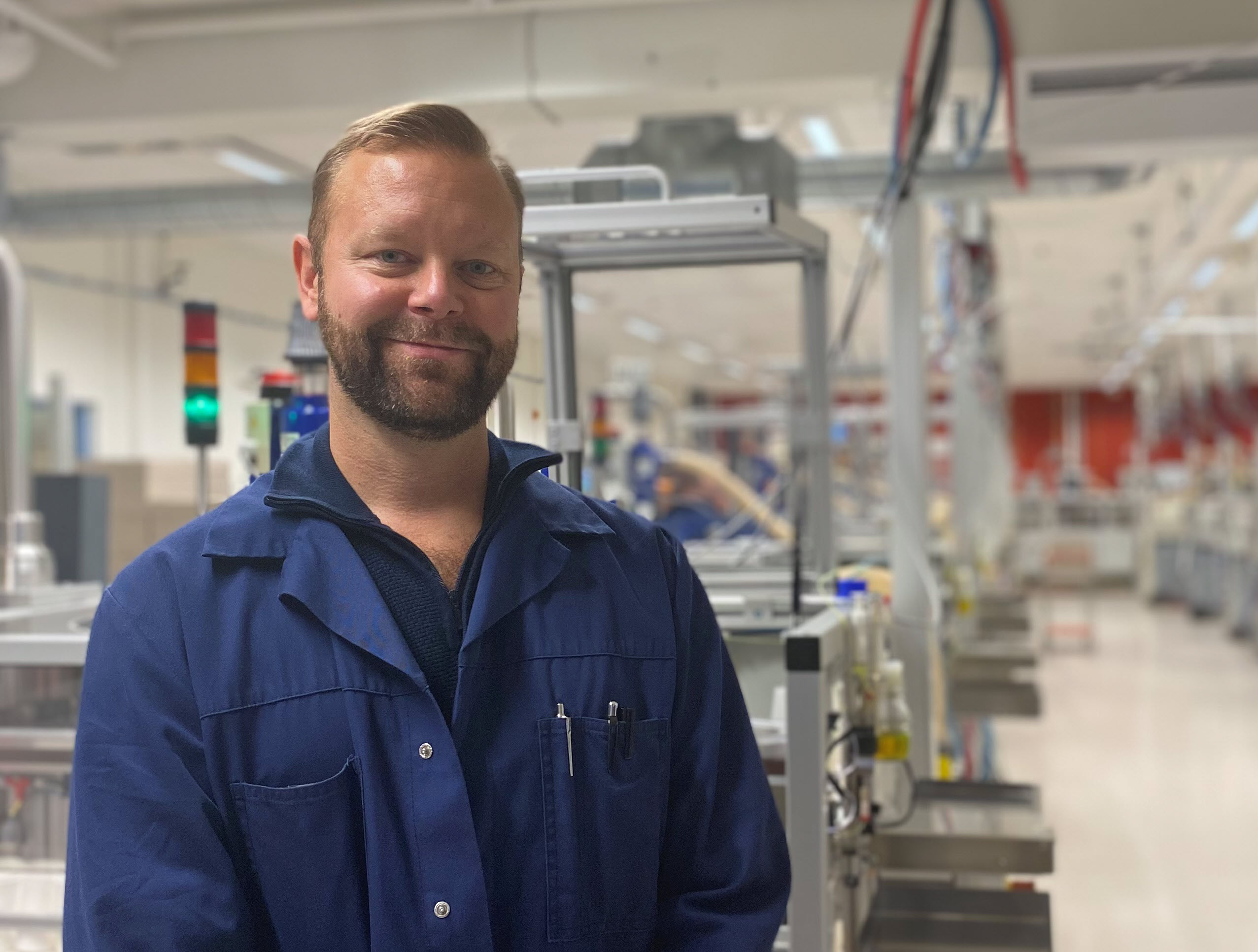
Henrik Pommer, who started at HemoCue as a machine operator 20 years ago and is now a production manager, explained that the secret to reproducing so many cuvettes is the process of injection molding. “The molding process is where the magic happens. But everything must work perfectly,” explained Henrik. “There are several parameters that have to be exactly right. Pressure, temperature, timing and much more all have to align correctly to get a precise shape. There’s actually a lot that could go wrong.” And yet the entire molding process takes just 8 seconds. Once the cuvette comes out of the mold and it is filled with a reagent or detergent, it goes through a series of tests to ensure that it meets HemoCue’s exacting standards. These include: With all these checks, it would be easy to imagine that there are many errors found. Not so. Out of the 140 million+ cuvettes produced every year, 96% are flawless. For Henrik Pommer, there is more than professional pride in working with such precision machinery. Henrik explained that he donates blood regularly, both at work (HemoCue uses real blood to do research and test their analyzers!) and at the local blood bank. And each time, hemoglobin in his blood is measured using HemoCue products. On one occasion when donating blood at a clinic, his hemoglobin results came back alarmingly low. Doctors were immediately summoned to make sure Henrik was OK. He was tested again, and his hemoglobin was normal. It turned out that there was an issue with the bags that held his blood and had caused an inaccurate reading. “It was very reassuring to experience firsthand how our products help medical teams care for their patients,” said Henrik. “Fortunately, I was fine, but it confirmed just how much my work matters for others who are actually suffering from low hemoglobin.”Injection molding is the key to accuracy
Test it, test it, and test it again
Precision is personal
Henrik Pommer, who started at HemoCue as a machine operator 20 years ago and is now a production manager, explained that the secret to reproducing so many cuvettes is the process of injection molding. “The molding process is where the magic happens. But everything must work perfectly,” explained Henrik. “There are several parameters that have to be exactly right. Pressure, temperature, timing and much more all have to align correctly to get a precise shape. There’s actually a lot that could go wrong.” And yet the entire molding process takes just 8 seconds. Once the cuvette comes out of the mold and it is filled with a reagent or detergent, it goes through a series of tests to ensure that it meets HemoCue’s exacting standards. These include: With all these checks, it would be easy to imagine that there are many errors found. Not so. Out of the 140 million+ cuvettes produced every year, 96% are flawless. For Henrik Pommer, there is more than professional pride in working with such precision machinery. Henrik explained that he donates blood regularly, both at work (HemoCue uses real blood to do research and test their analyzers!) and at the local blood bank. And each time, hemoglobin in his blood is measured using HemoCue products. On one occasion when donating blood at a clinic, his hemoglobin results came back alarmingly low. Doctors were immediately summoned to make sure Henrik was OK. He was tested again, and his hemoglobin was normal. It turned out that there was an issue with the bags that held his blood and had caused an inaccurate reading. “It was very reassuring to experience firsthand how our products help medical teams care for their patients,” said Henrik. “Fortunately, I was fine, but it confirmed just how much my work matters for others who are actually suffering from low hemoglobin.”Injection molding is the key to accuracy
Test it, test it, and test it again
Precision is personal
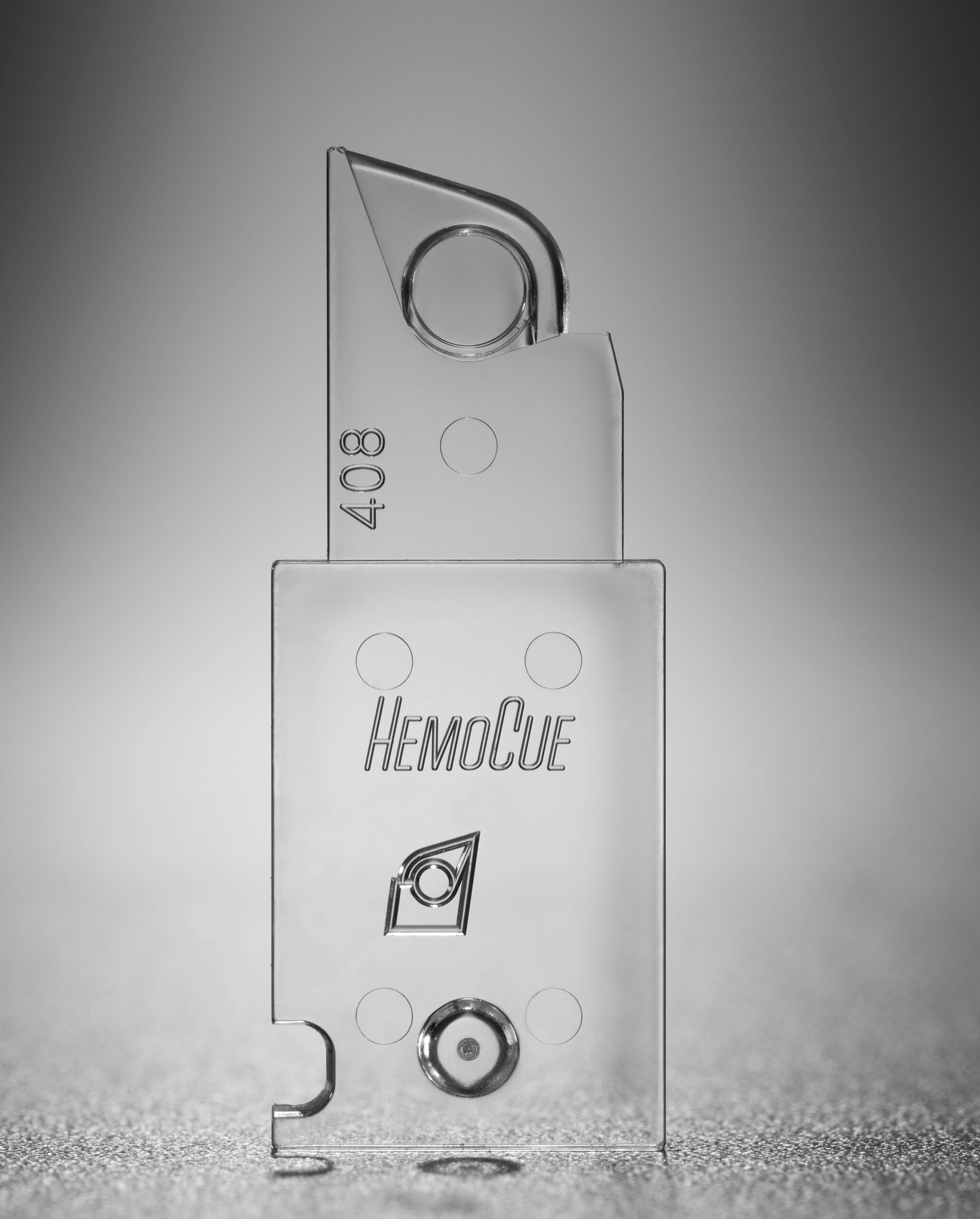
JUST HOW SMALL IS A MICROMETER?
Imagine something small, then reduce it by powers of 10!
The distance between the walls of the “eye” of HemoCue’s cuvettes is measured in micrometers. But what exactly does that mean?
A micrometer, or micron, is a unit of length in the International System of Units equalling 1×10−6 meter. In other words, a micrometer is one millionth of a meter, or one thousandth of a millimeter. In other other words, really small.
For comparison, the width of a human hair ranges between 20 and 200 micrometers. The micrometer is so small that it is used for measuring miniscule objects, such as biological cells and bacteria.
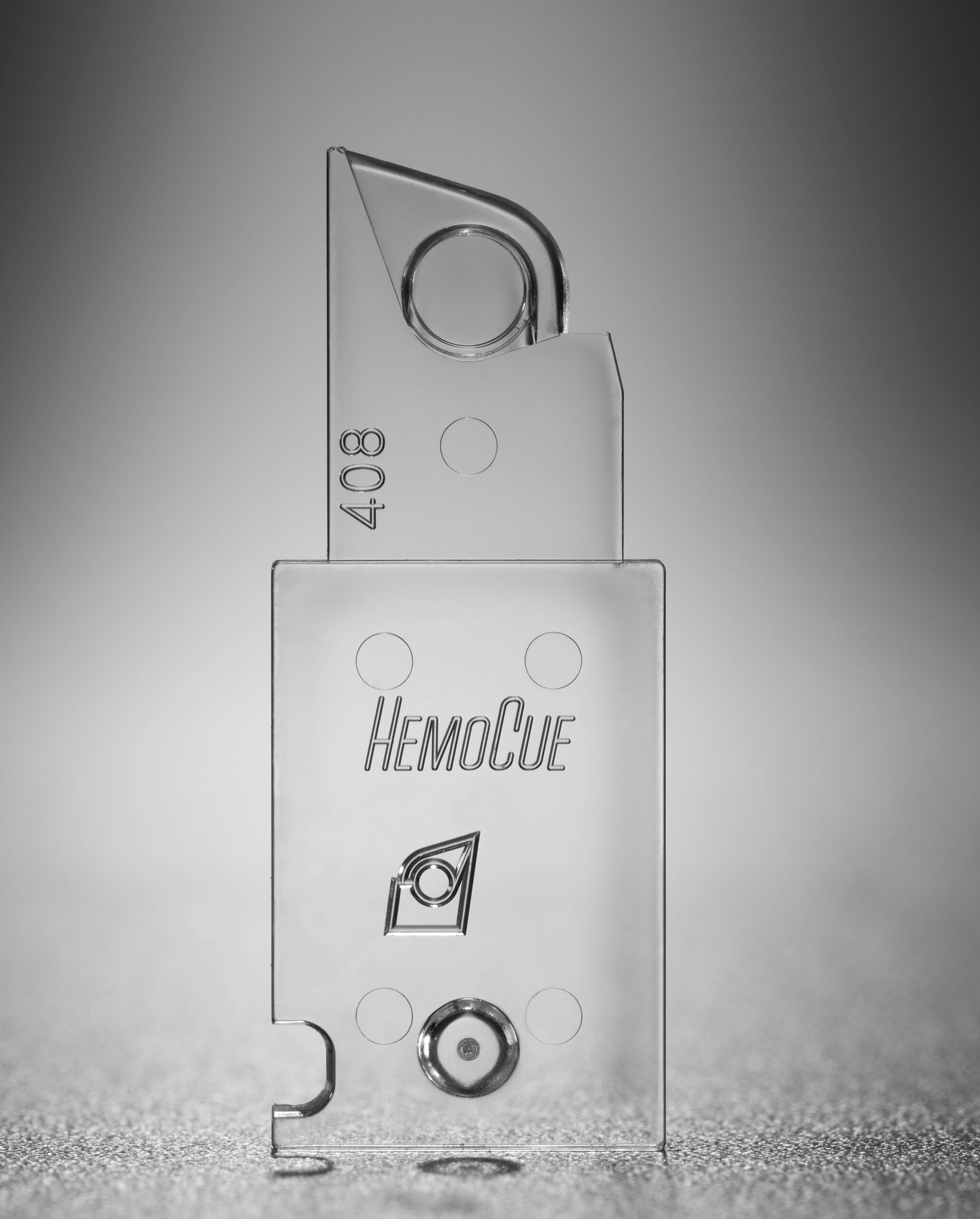
JUST HOW SMALL IS A MICROMETER?
Imagine something small, then reduce it by powers of 10!
The distance between the walls of the “eye” of HemoCue’s cuvettes is measured in micrometers. But what exactly does that mean?
A micrometer, or micron, is a unit of length in the International System of Units equalling 1×10−6 meter. In other words, a micrometer is one millionth of a meter, or one thousandth of a millimeter. In other other words, really small.
For comparison, the width of a human hair ranges between 20 and 200 micrometers. The micrometer is so small that it is used for measuring miniscule objects, such as biological cells and bacteria.